Bug Fixing
Understanding Carrier Furnace Error Code 31: Causes and Solutions
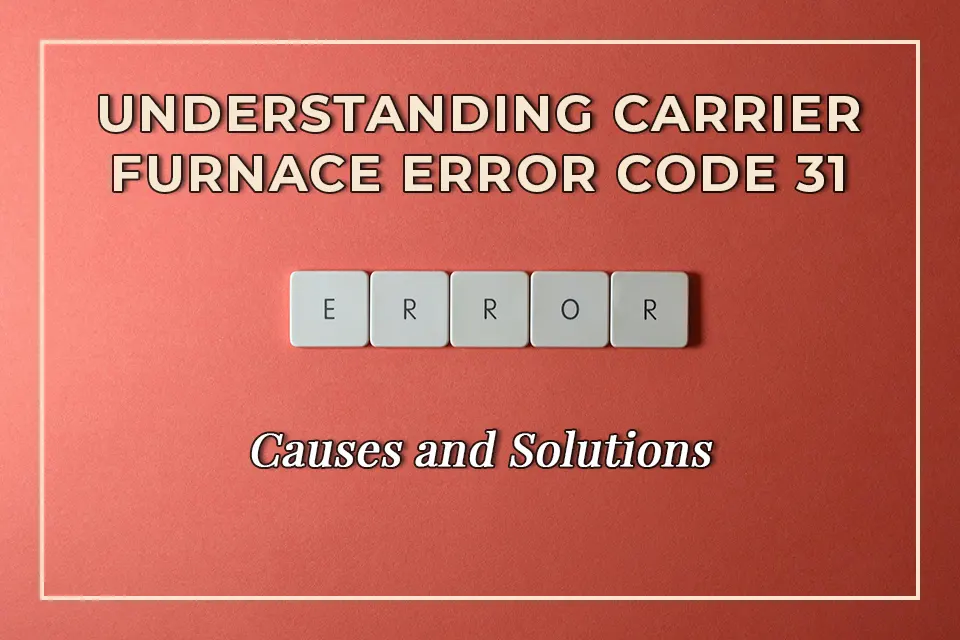
[ad_1]
In this article, we will discuss the carrier furnace error code 31, its causes, and possible solutions. Understanding the error code and its implications can help you troubleshoot and resolve the issue without the need for professional assistance, saving you time and money. We will provide you with simple, straightforward explanations and practical tips for addressing this error code, allowing you to restore your furnace to proper working condition as quickly as possible.
What is Carrier Furnace Error Code 31?
Carrier furnace error code 31 indicates a pressure switch fault. This fault occurs when the pressure switch fails to close or opens during the heat cycle. The pressure switch monitors the air pressure in the furnace and ensures that the combustion process is functioning properly. When the pressure switch malfunctions, it can disrupt the heating process and cause the furnace to shut down, triggering the error code 31.
Understanding the meaning of this error code is the first step in diagnosing and resolving the issue. By identifying the potential causes of the pressure switch fault, you can take appropriate action to address the problem and restore your furnace to normal operation.
What Causes Carrier Furnace Error Code 31?
The error code 31 on a Carrier furnace can be caused by a variety of factors. Some of the common causes include:
1. Clogged Vent Pipes: The vent pipes that release combustion gases from the furnace may become blocked by debris or other obstructions, preventing proper airflow and causing the pressure switch to malfunction.
2. Pressure Switch Issues: The pressure switch itself may be faulty or defective, leading to intermittent or persistent problems with closing or opening during the heat cycle.
3. Condensate Drain Problems: If the condensate drain line is clogged or obstructed, it can disrupt the proper drainage of condensate from the furnace, affecting the pressure switch operation.
By examining these potential causes and conducting a thorough inspection of your furnace, you can pinpoint the source of the error code 31 and take the necessary steps to address the underlying issue.
How to Resolve Carrier Furnace Error Code 31?
Resolving Carrier furnace error code 31 involves troubleshooting the potential causes and implementing the appropriate solutions. Here are some steps you can take to resolve this issue:
1. Check Vent Pipes: Inspect the vent pipes for any blockages or obstructions. Clear any debris or foreign objects that may be obstructing the airflow. Ensure that the vent pipes are free from any restrictions that could impede proper ventilation.
2. Inspect Pressure Switch: Check the pressure switch for any signs of damage or malfunction. If necessary, replace the pressure switch with a new one to ensure proper operation during the heat cycle.
3. Clean Condensate Drain: Clear any clogs or blockages in the condensate drain line to allow for unobstructed drainage of condensate from the furnace. This will help prevent pressure switch issues related to condensate backup.
By addressing these potential solutions, you can effectively resolve the error code 31 on your Carrier furnace and restore its proper functioning. However, if you are unsure about performing these tasks, it is recommended to seek professional assistance to avoid any safety risks or further damage to the furnace.
Conclusion
Understanding Carrier furnace error code 31 and its potential causes is essential for troubleshooting and resolving this issue effectively. By identifying the source of the pressure switch fault and implementing the appropriate solutions, you can restore your furnace to normal operation and avoid the need for costly repairs or replacements. Remember to prioritize safety and seek professional assistance if you are uncertain about performing any maintenance or repair tasks on your furnace.
FAQs
1. Can I reset the furnace to clear error code 31?
No, simply resetting the furnace may not clear error code 31, as it is likely caused by specific issues such as pressure switch faults, vent pipe blockages, or condensate drain problems. It is important to identify and address these underlying issues to resolve the error code.
2. How often should I inspect my furnace for potential issues?
Regular preventive maintenance and inspections are recommended to ensure the proper functioning of your furnace. It is advisable to inspect your furnace at least once a year, preferably before the start of the heating season, to address any potential issues and prevent future breakdowns.
3. Can I clean the vent pipes and condensate drain myself?
While some simple maintenance tasks can be performed by homeowners, it is important to exercise caution and prioritize safety. If you are unsure about cleaning the vent pipes or condensate drain, it is best to seek professional assistance to avoid potential safety risks or damage to the furnace.
4. Why is the pressure switch so important in furnace operation?
The pressure switch plays a crucial role in monitoring the air pressure in the furnace and ensuring the proper combustion process. If the pressure switch malfunctions, it can disrupt the heating cycle and lead to error code 31, indicating a potential issue that needs to be addressed for the furnace to operate efficiently.
5. What should I do if I am unable to resolve error code 31 on my furnace?
If you are unable to resolve error code 31 on your furnace or are uncertain about troubleshooting and repairs, it is recommended to seek professional assistance from a qualified HVAC technician. Attempting DIY repairs beyond your comfort level may lead to further issues or safety risks.
[ad_2]
Bug Fixing
What Does a Flashing Green Light on My Lennox Furnace Mean?
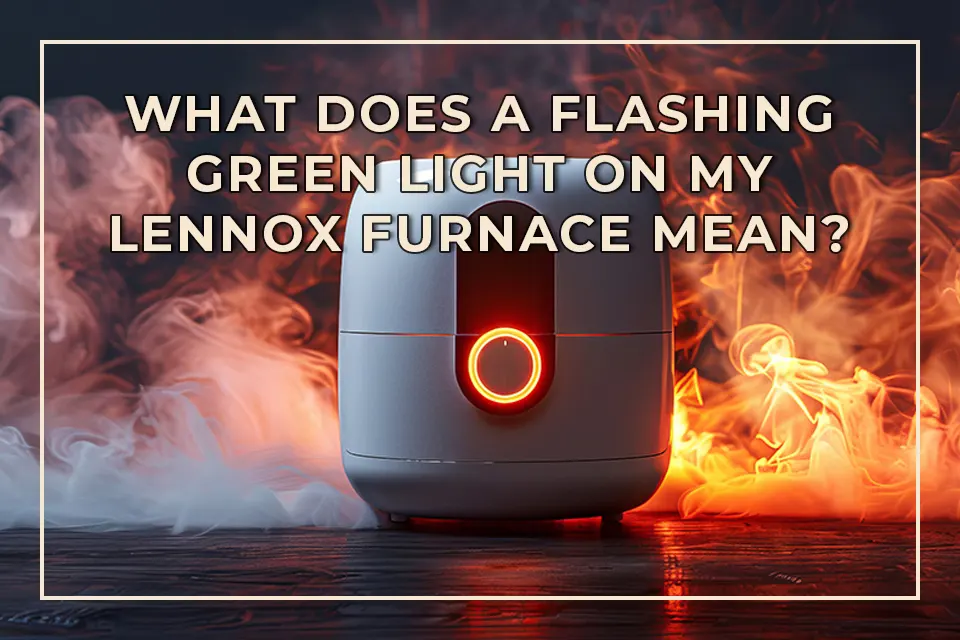
Understanding the functions and signals of your Lennox furnace is crucial for maintaining a comfortable and safe home environment. A flashing green light on your Lennox furnace can indicate various operational states or issues that need your attention. This guide will help you decipher what that signal means and what steps to take next.
The Importance of the Flashing Green Light
The furnace control panel features essential indicators, including the green light. This light serves as your furnace’s communication tool, alerting you to its operational status. A steady green light usually indicates that the furnace is functioning normally, while a flashing green light requires further investigation.
When you notice a blinking green light, it typically pertains to the furnace’s diagnostic system. Understanding what the flashing signals mean can save you time and money in troubleshooting or professional repair services. Knowing how to interpret these signals can empower you as a homeowner to maintain your furnace efficiently.
Common Reasons for a Flashing Green Light
- Normal Operation: While a steady green light often means everything is running well, a flashing green light is not automatically a cause for concern. This could indicate the furnace is starting a ignition process, signaling that it’s preparing to heat your home.
- Furnace Status Checks: A flashing green light may also mean the furnace is entering or going through a self-diagnostic check. In this case, the system examines its components for proper operation. Generally, the light may blink a specific number of times before turning steady, which can provide clues about issues.
- Error Codes: Different sequences of flashing patterns can represent unique error codes. For example, a flashing green light followed by a pause can indicate a problem with gas pressure or an issue with the ignition system. Refer to your user manual or manufacturer guidance to decode the pattern accurately.
Troubleshooting Steps When You See a Flashing Green Light
If you notice a flashing green light on your Lennox furnace, it’s essential to stay calm. Here’s how you might approach the situation:
1. Consult the Owner’s Manual: Your first step should be checking the furnace’s user manual for specific diagnostics. The manual often contains a section dedicated to interpreting light signals and error codes that are unique to your model.
2. Resetting the Furnace: Sometimes, a simple reset can clear temporary errors. Turn the furnace off at the thermostat, wait for a few moments, and then turn it back on. If the green light remains flashing, further investigation is needed.
3. Examine the Air Filters and Vents: Clogged air filters or blocked vents can create issues with airflow, leading to operational problems. Check and replace any dirty filters and ensure all vents are open and unobstructed.
Professional Intervention: When is it Necessary?
If troubleshooting doesn’t resolve the issue, it may be time to involve a professional. A flashing green light can indicate a more serious problem that requires specialized skills and tools to diagnose appropriately.
1. Persistent Flashing: If the green light doesn’t revert to a steady signal despite following the troubleshooting steps, it’s essential to seek help. Persistent issues often indicate underlying problems that only a certified technician can address safely.
2. Complex Errors: Some errors linked with a flashing green light involve complex furnace systems, such as ignition failures, gas supply issues, or electrical anomalies. Professionals can conduct in-depth diagnostics to identify the root cause and recommend repairs.
3. Routine Maintenance: Regardless of the flashing light, it’s wise to schedule regular furnace maintenance. Professional servicing can prevent future issues, optimize performance, and extend the lifespan of your system.
Understanding the Role of the Circuit Board
Modern Lennox furnaces feature advanced circuit boards that manage their operation. The circuit board interprets how the furnace functions, detects problems, and communicates them through the status lights.
1. Flashing Patterns: Each flashing pattern indicative of a specific state or issue is comprehended by the circuit board’s diagnostic program. If your furnace’s flashing green light signals a persistent issue, this could suggest a malfunctioning circuit board.
2. Updating Components: Circuit boards may require updates or replacement, especially in older models. Discussing with a professional can help you find the right solution if such a scenario is responsible for the flashing signal.
Enhancing Your Understanding for Future Repairs
A little knowledge can go a long way when it comes to repairing your heater. By understanding common indicators like the flashing green light, you can approach possible problems with confidence.
1. Documenting Patterns: Keeping a record of your furnace’s behaviors, including how the lights flash or change over time, can help service technicians understand the history of your unit, potentially leading to quicker resolutions.
2. Learning as You Go: Like many appliances in your home, regular interaction with your furnace can enhance your understanding. Familiarizing yourself with its sounds, lights, and operations can prepare you for recognizing when things are off, increasing your effectiveness in troubleshooting.
Conclusion
A flashing green light on your Lennox furnace plays a critical role in maintaining your home’s heating system’s health. While it can indicate several issues—from normal operational checks to the need for repairs—being informed helps you navigate the situation with confidence. Adopting a proactive stance through regular maintenance and understanding your unit’s communication signals can effectively prolong its lifespan.
FAQs
- What should I do if the flashing light continues after troubleshooting?
If the green light remains flashing after performing troubleshooting steps, it’s advisable to call a professional technician to diagnose and repair the underlying issue. - Can a dirty air filter cause a flashing light?
Yes, a dirty air filter can impede airflow, potentially causing your Lennox furnace to malfunction and trigger a flashing light. - How often should I perform maintenance on my furnace?
Regular maintenance is recommended at least once a year, preferably before the onset of colder weather, to ensure your furnace operates efficiently. - Is it safe to ignore the flashing green light?
Ignoring a flashing green light is not advisable, as it may indicate deeper issues within your furnace that could affect safety and efficiency. - Where can I find the diagnostic code for my specific furnace model?
You can find the diagnostic codes in your owner’s manual or on the Lennox website. Checking for your specific model’s guide will provide the necessary reference for error codes and light sequences.
Bug Fixing
Understanding the Basics: A Guide to 240V 24V Transformer Wiring Diagrams
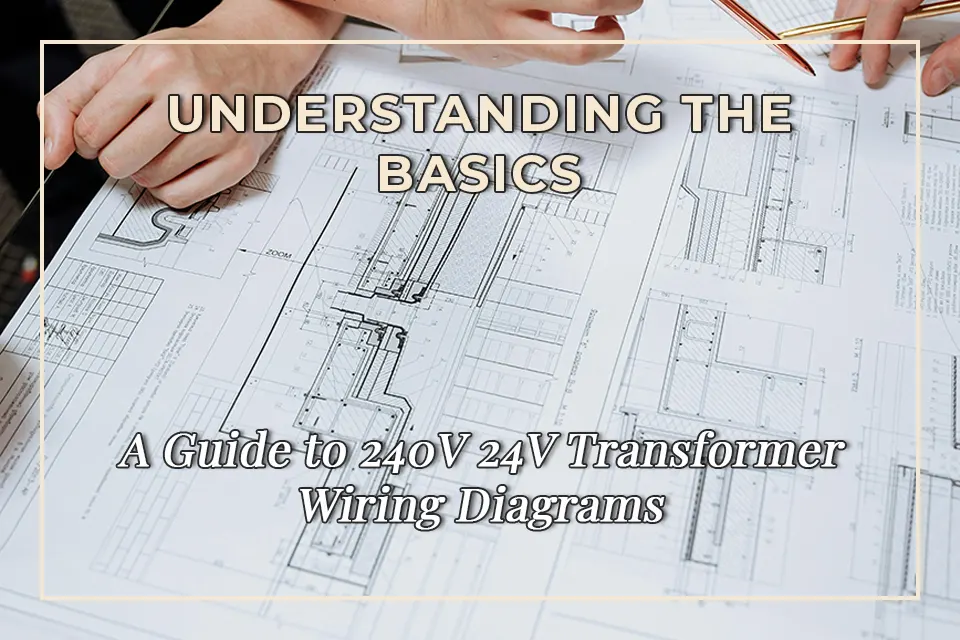
[ad_1]
Looking to understand the basics of 240V 24V transformer wiring diagrams? This guide will help you navigate the ins and outs of transformer wiring, from understanding the components to making the right connections. Whether you’re a DIY enthusiast or a professional electrician, this article will provide you with the knowledge you need to tackle transformer wiring with confidence.
What is a 240V 24V Transformer and How Does It Work?
A 240V 24V transformer is a type of electrical transformer that is used to step down the voltage from a 240V power source to a 24V output. It consists of primary and secondary coils, with the primary coil receiving the 240V input and the secondary coil delivering the 24V output. The transformer works on the principle of electromagnetic induction, where the changing magnetic field induces a voltage in the secondary coil, resulting in a different voltage level than the input.
When the transformer is properly connected, it can provide the necessary voltage for low-voltage applications, such as powering thermostats, doorbells, and other control systems. Understanding the basics of how a 240V 24V transformer works is crucial for correctly wiring it in various applications.
How to Read a 240V 24V Transformer Wiring Diagram
Wiring diagrams for 240V 24V transformers typically show the connections between the primary and secondary coils, as well as any additional components such as fuses, switches, or terminals. The diagram will help you understand how to make the correct connections and ensure the transformer is properly installed.
When reading a wiring diagram, it’s important to pay attention to the color-coding of the wires, as well as any labels or markings on the transformer itself. This will help you identify the primary and secondary coils, as well as any other connections that need to be made. Following the wiring diagram accurately is essential for a safe and functional installation of the transformer.
Step-by-Step Guide to Wiring a 240V 24V Transformer
When it comes to wiring a 240V 24V transformer, it’s important to follow a step-by-step process to ensure the job is done correctly. Start by identifying the primary and secondary coils on the transformer, as well as any additional components that need to be connected. Then, make the necessary connections according to the wiring diagram, paying close attention to the color-coding and labeling as mentioned earlier.
After making the connections, it’s crucial to test the transformer to ensure it is functioning properly and delivering the correct voltage. This can be done using a multimeter to measure the output voltage and ensure it matches the specified level. Once the transformer is confirmed to be working as intended, it can be integrated into the relevant electrical system for its intended purpose.
Common Mistakes to Avoid When Wiring a 240V 24V Transformer
One of the most common mistakes when wiring a 240V 24V transformer is misidentifying the primary and secondary coils, leading to incorrect connections and potential damage to the transformer. It’s important to carefully review the wiring diagram and any labeling on the transformer to avoid this mistake. Additionally, using incorrect wire sizes or neglecting proper insulation can lead to safety hazards and diminished performance.
Another mistake to avoid is overlooking the need for proper grounding and protection measures, especially when working with higher voltage levels. Ensuring that the transformer installation complies with electrical codes and safety standards is essential for preventing accidents and ensuring the longevity of the equipment.
Conclusion
Understanding the basics of 240V 24V transformer wiring diagrams is essential for anyone working with electrical systems, from DIY enthusiasts to professionals. By grasping the fundamental principles of how these transformers work, reading wiring diagrams, and following a proper installation process, you can confidently tackle transformer wiring projects and ensure safe and reliable operation.
FAQs
Q: Can I use a 240V 24V transformer for other voltage levels?
A: No, a 240V 24V transformer is specifically designed to step down the voltage from 240V to 24V. Attempting to use it for other voltage levels can result in damage to the transformer and potential safety hazards.
Q: What should I do if I encounter a wiring diagram with unclear markings?
A: If you come across a wiring diagram with unclear markings, it’s best to consult the manufacturer’s documentation or seek guidance from an experienced electrician to ensure the correct connections are made.
Q: Are there any specific safety precautions to take when wiring a 240V 24V transformer?
A: Yes, it’s important to take precautions such as wearing insulated gloves, ensuring proper grounding, and following electrical codes to minimize the risk of electric shock and other safety hazards.
Q: Can I wire a 240V 24V transformer without a wiring diagram?
A: While it’s not recommended, it is possible to wire a transformer without a diagram if you have a thorough understanding of the transformer’s components and connections. However, using a wiring diagram is the best practice to ensure accuracy.
Q: What should I do if I suspect a problem with the transformer after it’s been wired?
A: If you suspect an issue with the transformer, such as incorrect voltage output or abnormal operation, it’s best to disconnect the power and seek assistance from a qualified electrician to diagnose and resolve the problem.
[ad_2]
Bug Fixing
The Dangers of Leaving an Ice Maker on Without Water: What You Need to Know
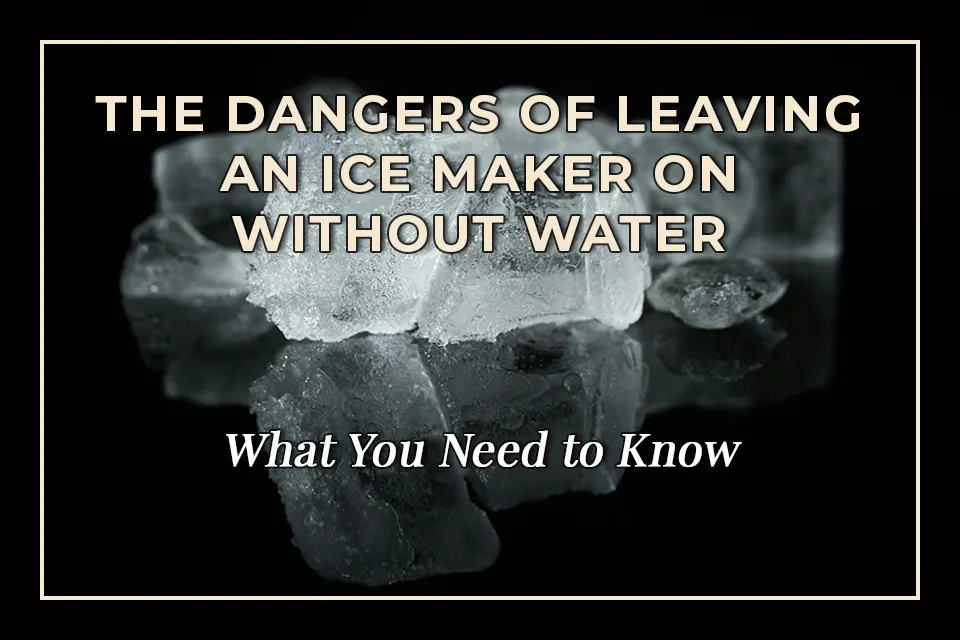
[ad_1]
Are you in the habit of leaving your ice maker turned on even when there’s no water in the machine? If so, you may not be aware of the potential dangers associated with this common practice. In this article, we’ll discuss the risks of leaving an ice maker on without water, and what you need to know to prevent potential damage to your appliance. We’ll also provide some practical tips for maintaining your ice maker to avoid any costly repairs or replacements. Read on to learn more about the dangers of leaving an ice maker on without water, and how to avoid them.
What happens when you leave an ice maker on without water?
Leaving your ice maker turned on without water can lead to a range of issues that can affect the performance of the machine. One of the most common problems is the build-up of ice inside the ice maker, which can cause the machine to malfunction and stop producing ice. Additionally, the lack of water in the machine can also lead to the motor working harder, which can potentially cause overheating and damage to the appliance over time.
When an ice maker is left on without water, it can also lead to the development of mold and mildew inside the machine, as well as an unpleasant odor. This can not only affect the taste and quality of the ice produced but also pose potential health risks to those consuming the ice.
How to prevent damage to your ice maker
One of the most effective ways to prevent damage to your ice maker is to ensure that the machine is always turned off when there is no water supply. This simple step can help to avoid the build-up of ice, reduce the strain on the motor, and prevent the development of mold and mildew inside the machine.
Regularly cleaning and maintaining your ice maker is also essential to prevent damage and ensure optimal performance. This includes regularly removing any built-up ice and debris, as well as cleaning the interior of the machine to prevent the growth of mold and mildew. Following the manufacturer’s guidelines for maintenance and cleaning can help to extend the lifespan of your ice maker and reduce the likelihood of any costly repairs.
Can leaving an ice maker on without water cause damage to your home?
Leaving an ice maker on without water can potentially cause damage to your home, especially if the appliance malfunctions and leaks water. The build-up of ice in the machine can lead to excess water spilling onto the floor, which can result in water damage to your kitchen or surrounding areas. Additionally, if the motor overheats due to the lack of water, it can pose a fire hazard, which can be a serious risk to your home and safety.
To prevent any potential damage to your home, it’s essential to ensure that your ice maker is always turned off when not in use, and to regularly inspect the machine for any signs of leaks or malfunctions. If you notice any issues with your ice maker, it’s important to address them immediately to prevent any further damage to your home or appliance.
How can you tell if your ice maker has been damaged due to lack of water?
There are several signs that may indicate that your ice maker has been damaged due to the lack of water. These can include a decrease in ice production, unusual noises coming from the machine, or a change in the taste or quality of the ice produced. If you notice any of these signs, it’s important to turn off your ice maker and inspect the machine for any visible damage, such as ice build-up or leaks.
If you suspect that your ice maker has been damaged due to the lack of water, it’s essential to contact a professional appliance repair technician to assess the extent of the damage and make any necessary repairs. Ignoring potential damage to your ice maker can lead to further issues and potentially result in the need for a costly replacement.
Conclusion
Leaving an ice maker on without water can pose several risks, including potential damage to the appliance and your home. To prevent any issues, it’s important to ensure that your ice maker is always turned off when not in use, and to regularly clean and maintain the machine to prevent the build-up of ice and mold. By following these simple tips, you can help to prolong the lifespan of your ice maker and avoid any costly repairs or replacements.
FAQs
1. Can leaving an ice maker on without water cause damage to the appliance?
Yes, leaving an ice maker on without water can lead to the build-up of ice, strain on the motor, and potential damage to the appliance over time. It can also lead to the development of mold and mildew inside the machine, affecting the taste and quality of the ice produced.
2. How can I prevent potential damage to my ice maker?
To prevent potential damage to your ice maker, ensure that the machine is always turned off when there is no water supply. Additionally, regularly cleaning and maintaining your ice maker can help to prevent the build-up of ice and mold, ensuring optimal performance.
3. Can leaving an ice maker on without water cause damage to my home?
Leaving an ice maker on without water can potentially cause damage to your home if the appliance malfunctions and leaks water onto the floor. It can also pose a fire hazard if the motor overheats due to the lack of water.
4. How can I tell if my ice maker has been damaged due to lack of water?
Signs of potential damage to your ice maker due to the lack of water can include a decrease in ice production, unusual noises coming from the machine, and a change in the taste or quality of the ice produced. If you notice any of these signs, it’s important to turn off your ice maker and inspect the machine for any visible damage.
5. What should I do if I suspect my ice maker has been damaged?
If you suspect that your ice maker has been damaged due to the lack of water, it’s essential to contact a professional appliance repair technician to assess the extent of the damage and make any necessary repairs. Ignoring potential damage to your ice maker can lead to further issues and potentially result in the need for a costly replacement.
[ad_2]
- DIY Closet2 years ago
How to troubleshoot and reset the red light on your Aquaguard AG 3000E
- DIY Closet2 years ago
How to Install a Drop-In Sink Without Clips: A Step-by-Step Guide
- Bug Fixing1 year ago
Understanding the Cost of Furnace Collector Box Replacement: What to Expect
- DIY Closet1 year ago
Pergola Design: Understanding the Maximum Span for 6×6 Beams
- DIY Closet2 years ago
The Best Nails for Luan: A Comprehensive Guide
- Bug Fixing1 year ago
Pigtail vs Daisy Chain Outlets: Which is Better for Your Home?
- DIY Closet2 years ago
How to Build a Free Standing 6×6 Post Swing Set: A Step-by-Step Guide
- DIY Closet1 year ago
Understanding the Benefits of a 400 Amp Meter Base with Two 200 Amp Disconnects