Bug Fixing
Understanding Carrier Code 21 Gas Heating Lockout: Causes and Solutions
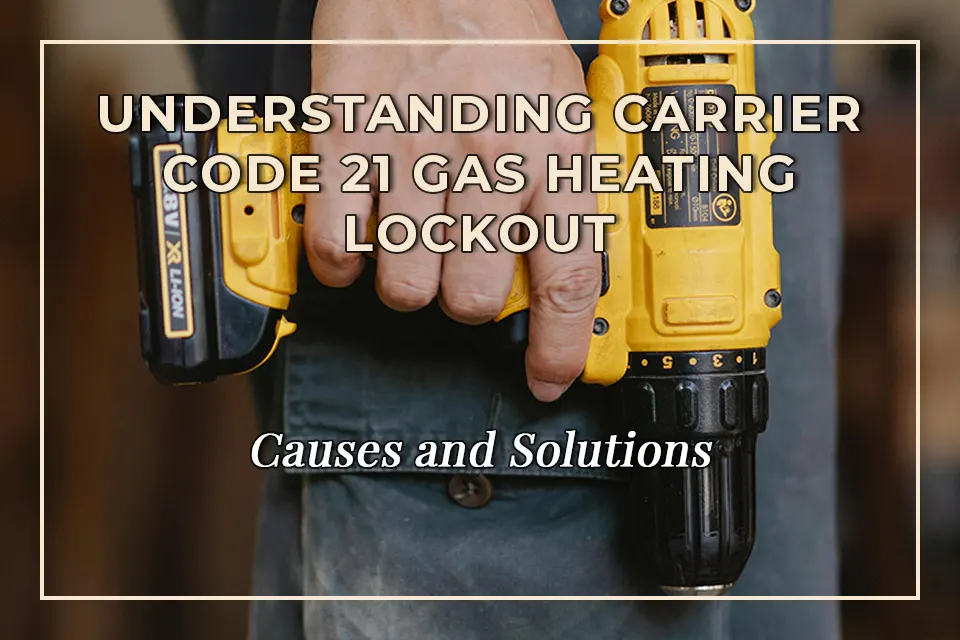
[ad_1]
In this article, we will discuss the causes and potential solutions for Carrier Code 21 gas heating lockout. We will break down this common issue, providing an overview of why it occurs and what steps you can take to resolve it. By the end of this article, you should have a better understanding of Carrier Code 21 and feel confident in troubleshooting and fixing this problem if it arises in your gas heating system.
What is Carrier Code 21 Gas Heating Lockout?
Carrier Code 21 is a common issue that can occur in gas heating systems. When this code is displayed, it indicates that the furnace has entered a lockout state, meaning it has shut down and will not restart without intervention. This lockout is a safety mechanism designed to protect the system from further damage or potentially hazardous conditions.
There are a few potential reasons why a gas heating system may enter lockout mode and display Carrier Code 21. Some common causes include issues with the ignition, flame sensor, or pressure switch. Additionally, a dirty air filter, malfunctioning thermostat, or lack of fuel supply can also trigger this lockout code.
What Causes Carrier Code 21 Gas Heating Lockout?
One of the primary causes of Carrier Code 21 is a lack of proper ignition. If the system is unable to ignite the gas to produce heat, it will enter lockout mode to prevent potentially dangerous conditions. This can be due to a faulty igniter, gas valve, or even a clogged burner.
Another potential cause is a malfunctioning flame sensor. The flame sensor is responsible for detecting the presence of a flame. If it fails to do so, the system will shut down to prevent the release of unburned gas, which could pose a safety risk.
In addition, issues with the pressure switch can also trigger Carrier Code 21. The pressure switch ensures that the system has proper airflow for combustion. If the pressure switch detects an abnormal air pressure, it will cause the system to lock out.
How to Resolve Carrier Code 21 Gas Heating Lockout?
When dealing with Carrier Code 21, it is essential to address the underlying cause of the lockout. Start by checking the fuel supply to ensure that there are no issues with gas flow or pressure. Verify that the gas valve is open and that there are no obstructions in the supply line. If everything appears to be in order, move on to inspecting the ignition and flame sensor.
Inspect the igniter and ensure that it is in working condition. If it appears worn or damaged, it may need to be replaced. Clean the flame sensor to remove any buildup that could be interfering with its ability to detect the flame. Additionally, check the pressure switch for any blockages or malfunctions that may be causing the lockout.
If the lockout persists after addressing these initial issues, it may be necessary to replace any faulty components or seek professional assistance. In some cases, the thermostat or air filter may also need attention to ensure proper system operation and prevent future lockouts.
Conclusion
Carrier Code 21 gas heating lockout can be a frustrating issue to encounter, but with a basic understanding of its causes and solutions, you can confidently troubleshoot and resolve this problem. By addressing issues with ignition, flame sensor, pressure switch, and other potential culprits, you can resolve the lockout and restore your gas heating system to proper working order. Regular maintenance and attention to system components can help prevent future occurrences of Carrier Code 21, keeping your home warm and comfortable throughout the colder months.
FAQs
1. Can I reset the system to clear Carrier Code 21?
While it may be possible to reset the system to clear Carrier Code 21 temporarily, it is essential to address the underlying cause of the lockout to prevent it from happening again. Resetting the system without fixing the issue may result in further lockouts and potential safety hazards.
2. Why is the flame sensor important in gas heating systems?
The flame sensor is crucial in gas heating systems as it detects the presence of a flame. If the sensor fails, the system may release unburned gas, posing a safety risk. Regular maintenance and cleaning of the flame sensor can help ensure its proper function.
3. Can I clean the igniter myself?
Cleaning the igniter can be done as part of regular maintenance. However, if the igniter appears damaged or worn, it may need to be replaced. It is important to follow proper safety procedures and, if unsure, consult a professional for assistance.
4. What should I do if none of the troubleshooting steps resolve the lockout?
If the lockout persists after attempting the troubleshooting steps, or if you are unsure about performing the necessary maintenance, it is best to seek professional assistance. A certified technician can diagnose and resolve the issue to ensure safe and proper operation of your gas heating system.
5. How can I prevent future lockouts in my gas heating system?
Regular maintenance, including cleaning and inspection of system components, can help prevent future lockouts. Additionally, ensuring proper airflow, fuel supply, and thermostat operation can contribute to the smooth and efficient function of your gas heating system.
[ad_2]
Bug Fixing
What Does a Flashing Green Light on My Lennox Furnace Mean?
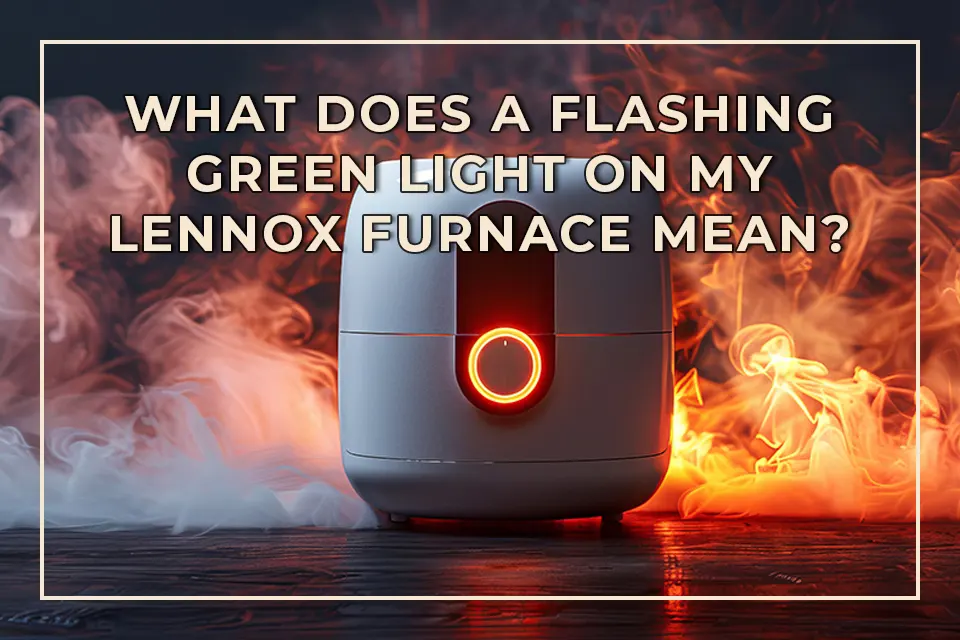
Understanding the functions and signals of your Lennox furnace is crucial for maintaining a comfortable and safe home environment. A flashing green light on your Lennox furnace can indicate various operational states or issues that need your attention. This guide will help you decipher what that signal means and what steps to take next.
The Importance of the Flashing Green Light
The furnace control panel features essential indicators, including the green light. This light serves as your furnace’s communication tool, alerting you to its operational status. A steady green light usually indicates that the furnace is functioning normally, while a flashing green light requires further investigation.
When you notice a blinking green light, it typically pertains to the furnace’s diagnostic system. Understanding what the flashing signals mean can save you time and money in troubleshooting or professional repair services. Knowing how to interpret these signals can empower you as a homeowner to maintain your furnace efficiently.
Common Reasons for a Flashing Green Light
- Normal Operation: While a steady green light often means everything is running well, a flashing green light is not automatically a cause for concern. This could indicate the furnace is starting a ignition process, signaling that it’s preparing to heat your home.
- Furnace Status Checks: A flashing green light may also mean the furnace is entering or going through a self-diagnostic check. In this case, the system examines its components for proper operation. Generally, the light may blink a specific number of times before turning steady, which can provide clues about issues.
- Error Codes: Different sequences of flashing patterns can represent unique error codes. For example, a flashing green light followed by a pause can indicate a problem with gas pressure or an issue with the ignition system. Refer to your user manual or manufacturer guidance to decode the pattern accurately.
Troubleshooting Steps When You See a Flashing Green Light
If you notice a flashing green light on your Lennox furnace, it’s essential to stay calm. Here’s how you might approach the situation:
1. Consult the Owner’s Manual: Your first step should be checking the furnace’s user manual for specific diagnostics. The manual often contains a section dedicated to interpreting light signals and error codes that are unique to your model.
2. Resetting the Furnace: Sometimes, a simple reset can clear temporary errors. Turn the furnace off at the thermostat, wait for a few moments, and then turn it back on. If the green light remains flashing, further investigation is needed.
3. Examine the Air Filters and Vents: Clogged air filters or blocked vents can create issues with airflow, leading to operational problems. Check and replace any dirty filters and ensure all vents are open and unobstructed.
Professional Intervention: When is it Necessary?
If troubleshooting doesn’t resolve the issue, it may be time to involve a professional. A flashing green light can indicate a more serious problem that requires specialized skills and tools to diagnose appropriately.
1. Persistent Flashing: If the green light doesn’t revert to a steady signal despite following the troubleshooting steps, it’s essential to seek help. Persistent issues often indicate underlying problems that only a certified technician can address safely.
2. Complex Errors: Some errors linked with a flashing green light involve complex furnace systems, such as ignition failures, gas supply issues, or electrical anomalies. Professionals can conduct in-depth diagnostics to identify the root cause and recommend repairs.
3. Routine Maintenance: Regardless of the flashing light, it’s wise to schedule regular furnace maintenance. Professional servicing can prevent future issues, optimize performance, and extend the lifespan of your system.
Understanding the Role of the Circuit Board
Modern Lennox furnaces feature advanced circuit boards that manage their operation. The circuit board interprets how the furnace functions, detects problems, and communicates them through the status lights.
1. Flashing Patterns: Each flashing pattern indicative of a specific state or issue is comprehended by the circuit board’s diagnostic program. If your furnace’s flashing green light signals a persistent issue, this could suggest a malfunctioning circuit board.
2. Updating Components: Circuit boards may require updates or replacement, especially in older models. Discussing with a professional can help you find the right solution if such a scenario is responsible for the flashing signal.
Enhancing Your Understanding for Future Repairs
A little knowledge can go a long way when it comes to repairing your heater. By understanding common indicators like the flashing green light, you can approach possible problems with confidence.
1. Documenting Patterns: Keeping a record of your furnace’s behaviors, including how the lights flash or change over time, can help service technicians understand the history of your unit, potentially leading to quicker resolutions.
2. Learning as You Go: Like many appliances in your home, regular interaction with your furnace can enhance your understanding. Familiarizing yourself with its sounds, lights, and operations can prepare you for recognizing when things are off, increasing your effectiveness in troubleshooting.
Conclusion
A flashing green light on your Lennox furnace plays a critical role in maintaining your home’s heating system’s health. While it can indicate several issues—from normal operational checks to the need for repairs—being informed helps you navigate the situation with confidence. Adopting a proactive stance through regular maintenance and understanding your unit’s communication signals can effectively prolong its lifespan.
FAQs
- What should I do if the flashing light continues after troubleshooting?
If the green light remains flashing after performing troubleshooting steps, it’s advisable to call a professional technician to diagnose and repair the underlying issue. - Can a dirty air filter cause a flashing light?
Yes, a dirty air filter can impede airflow, potentially causing your Lennox furnace to malfunction and trigger a flashing light. - How often should I perform maintenance on my furnace?
Regular maintenance is recommended at least once a year, preferably before the onset of colder weather, to ensure your furnace operates efficiently. - Is it safe to ignore the flashing green light?
Ignoring a flashing green light is not advisable, as it may indicate deeper issues within your furnace that could affect safety and efficiency. - Where can I find the diagnostic code for my specific furnace model?
You can find the diagnostic codes in your owner’s manual or on the Lennox website. Checking for your specific model’s guide will provide the necessary reference for error codes and light sequences.
Bug Fixing
Understanding the Basics: A Guide to 240V 24V Transformer Wiring Diagrams
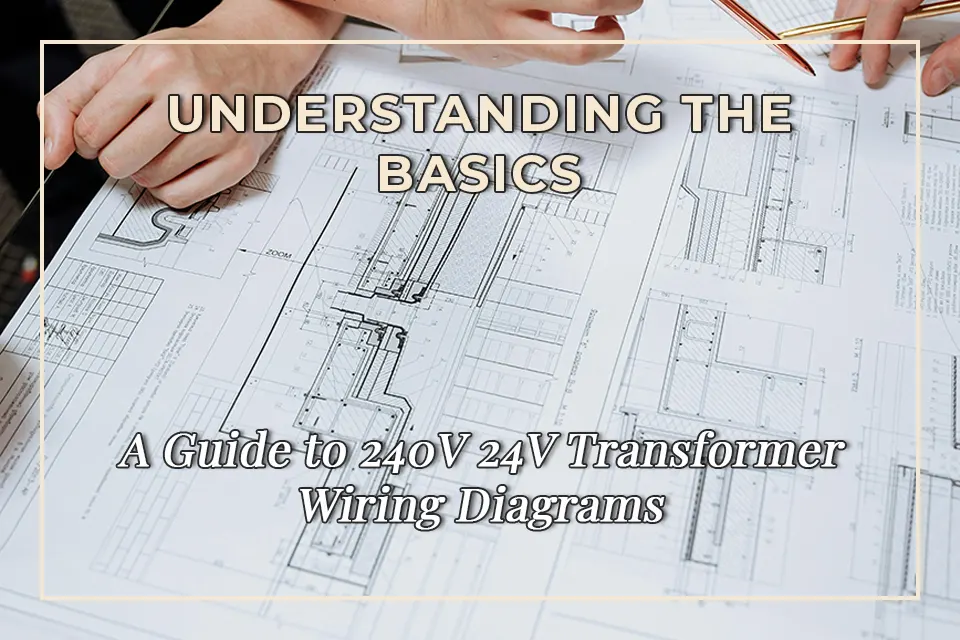
[ad_1]
Looking to understand the basics of 240V 24V transformer wiring diagrams? This guide will help you navigate the ins and outs of transformer wiring, from understanding the components to making the right connections. Whether you’re a DIY enthusiast or a professional electrician, this article will provide you with the knowledge you need to tackle transformer wiring with confidence.
What is a 240V 24V Transformer and How Does It Work?
A 240V 24V transformer is a type of electrical transformer that is used to step down the voltage from a 240V power source to a 24V output. It consists of primary and secondary coils, with the primary coil receiving the 240V input and the secondary coil delivering the 24V output. The transformer works on the principle of electromagnetic induction, where the changing magnetic field induces a voltage in the secondary coil, resulting in a different voltage level than the input.
When the transformer is properly connected, it can provide the necessary voltage for low-voltage applications, such as powering thermostats, doorbells, and other control systems. Understanding the basics of how a 240V 24V transformer works is crucial for correctly wiring it in various applications.
How to Read a 240V 24V Transformer Wiring Diagram
Wiring diagrams for 240V 24V transformers typically show the connections between the primary and secondary coils, as well as any additional components such as fuses, switches, or terminals. The diagram will help you understand how to make the correct connections and ensure the transformer is properly installed.
When reading a wiring diagram, it’s important to pay attention to the color-coding of the wires, as well as any labels or markings on the transformer itself. This will help you identify the primary and secondary coils, as well as any other connections that need to be made. Following the wiring diagram accurately is essential for a safe and functional installation of the transformer.
Step-by-Step Guide to Wiring a 240V 24V Transformer
When it comes to wiring a 240V 24V transformer, it’s important to follow a step-by-step process to ensure the job is done correctly. Start by identifying the primary and secondary coils on the transformer, as well as any additional components that need to be connected. Then, make the necessary connections according to the wiring diagram, paying close attention to the color-coding and labeling as mentioned earlier.
After making the connections, it’s crucial to test the transformer to ensure it is functioning properly and delivering the correct voltage. This can be done using a multimeter to measure the output voltage and ensure it matches the specified level. Once the transformer is confirmed to be working as intended, it can be integrated into the relevant electrical system for its intended purpose.
Common Mistakes to Avoid When Wiring a 240V 24V Transformer
One of the most common mistakes when wiring a 240V 24V transformer is misidentifying the primary and secondary coils, leading to incorrect connections and potential damage to the transformer. It’s important to carefully review the wiring diagram and any labeling on the transformer to avoid this mistake. Additionally, using incorrect wire sizes or neglecting proper insulation can lead to safety hazards and diminished performance.
Another mistake to avoid is overlooking the need for proper grounding and protection measures, especially when working with higher voltage levels. Ensuring that the transformer installation complies with electrical codes and safety standards is essential for preventing accidents and ensuring the longevity of the equipment.
Conclusion
Understanding the basics of 240V 24V transformer wiring diagrams is essential for anyone working with electrical systems, from DIY enthusiasts to professionals. By grasping the fundamental principles of how these transformers work, reading wiring diagrams, and following a proper installation process, you can confidently tackle transformer wiring projects and ensure safe and reliable operation.
FAQs
Q: Can I use a 240V 24V transformer for other voltage levels?
A: No, a 240V 24V transformer is specifically designed to step down the voltage from 240V to 24V. Attempting to use it for other voltage levels can result in damage to the transformer and potential safety hazards.
Q: What should I do if I encounter a wiring diagram with unclear markings?
A: If you come across a wiring diagram with unclear markings, it’s best to consult the manufacturer’s documentation or seek guidance from an experienced electrician to ensure the correct connections are made.
Q: Are there any specific safety precautions to take when wiring a 240V 24V transformer?
A: Yes, it’s important to take precautions such as wearing insulated gloves, ensuring proper grounding, and following electrical codes to minimize the risk of electric shock and other safety hazards.
Q: Can I wire a 240V 24V transformer without a wiring diagram?
A: While it’s not recommended, it is possible to wire a transformer without a diagram if you have a thorough understanding of the transformer’s components and connections. However, using a wiring diagram is the best practice to ensure accuracy.
Q: What should I do if I suspect a problem with the transformer after it’s been wired?
A: If you suspect an issue with the transformer, such as incorrect voltage output or abnormal operation, it’s best to disconnect the power and seek assistance from a qualified electrician to diagnose and resolve the problem.
[ad_2]
Bug Fixing
The Dangers of Leaving an Ice Maker on Without Water: What You Need to Know
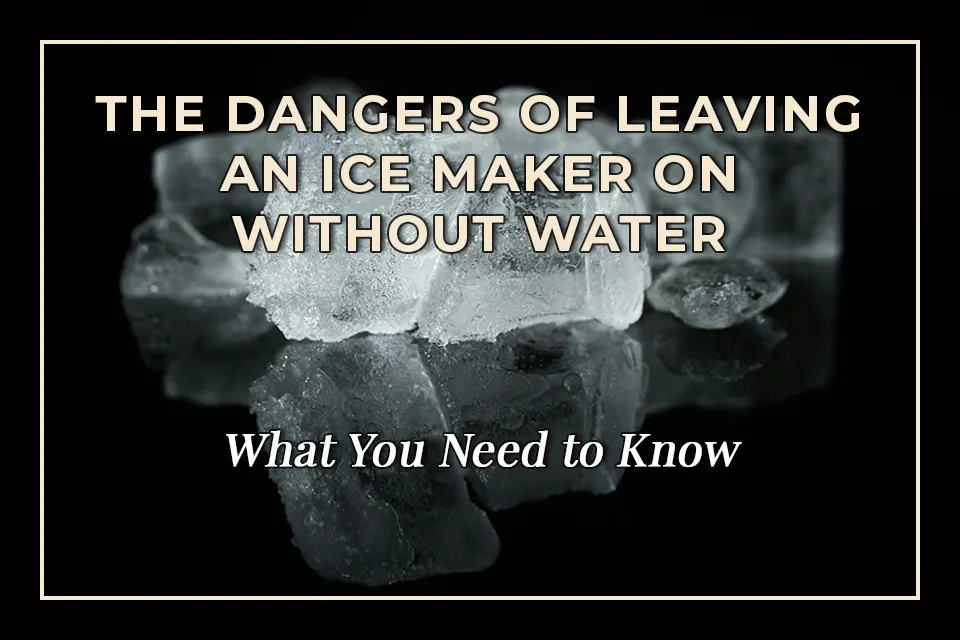
[ad_1]
Are you in the habit of leaving your ice maker turned on even when there’s no water in the machine? If so, you may not be aware of the potential dangers associated with this common practice. In this article, we’ll discuss the risks of leaving an ice maker on without water, and what you need to know to prevent potential damage to your appliance. We’ll also provide some practical tips for maintaining your ice maker to avoid any costly repairs or replacements. Read on to learn more about the dangers of leaving an ice maker on without water, and how to avoid them.
What happens when you leave an ice maker on without water?
Leaving your ice maker turned on without water can lead to a range of issues that can affect the performance of the machine. One of the most common problems is the build-up of ice inside the ice maker, which can cause the machine to malfunction and stop producing ice. Additionally, the lack of water in the machine can also lead to the motor working harder, which can potentially cause overheating and damage to the appliance over time.
When an ice maker is left on without water, it can also lead to the development of mold and mildew inside the machine, as well as an unpleasant odor. This can not only affect the taste and quality of the ice produced but also pose potential health risks to those consuming the ice.
How to prevent damage to your ice maker
One of the most effective ways to prevent damage to your ice maker is to ensure that the machine is always turned off when there is no water supply. This simple step can help to avoid the build-up of ice, reduce the strain on the motor, and prevent the development of mold and mildew inside the machine.
Regularly cleaning and maintaining your ice maker is also essential to prevent damage and ensure optimal performance. This includes regularly removing any built-up ice and debris, as well as cleaning the interior of the machine to prevent the growth of mold and mildew. Following the manufacturer’s guidelines for maintenance and cleaning can help to extend the lifespan of your ice maker and reduce the likelihood of any costly repairs.
Can leaving an ice maker on without water cause damage to your home?
Leaving an ice maker on without water can potentially cause damage to your home, especially if the appliance malfunctions and leaks water. The build-up of ice in the machine can lead to excess water spilling onto the floor, which can result in water damage to your kitchen or surrounding areas. Additionally, if the motor overheats due to the lack of water, it can pose a fire hazard, which can be a serious risk to your home and safety.
To prevent any potential damage to your home, it’s essential to ensure that your ice maker is always turned off when not in use, and to regularly inspect the machine for any signs of leaks or malfunctions. If you notice any issues with your ice maker, it’s important to address them immediately to prevent any further damage to your home or appliance.
How can you tell if your ice maker has been damaged due to lack of water?
There are several signs that may indicate that your ice maker has been damaged due to the lack of water. These can include a decrease in ice production, unusual noises coming from the machine, or a change in the taste or quality of the ice produced. If you notice any of these signs, it’s important to turn off your ice maker and inspect the machine for any visible damage, such as ice build-up or leaks.
If you suspect that your ice maker has been damaged due to the lack of water, it’s essential to contact a professional appliance repair technician to assess the extent of the damage and make any necessary repairs. Ignoring potential damage to your ice maker can lead to further issues and potentially result in the need for a costly replacement.
Conclusion
Leaving an ice maker on without water can pose several risks, including potential damage to the appliance and your home. To prevent any issues, it’s important to ensure that your ice maker is always turned off when not in use, and to regularly clean and maintain the machine to prevent the build-up of ice and mold. By following these simple tips, you can help to prolong the lifespan of your ice maker and avoid any costly repairs or replacements.
FAQs
1. Can leaving an ice maker on without water cause damage to the appliance?
Yes, leaving an ice maker on without water can lead to the build-up of ice, strain on the motor, and potential damage to the appliance over time. It can also lead to the development of mold and mildew inside the machine, affecting the taste and quality of the ice produced.
2. How can I prevent potential damage to my ice maker?
To prevent potential damage to your ice maker, ensure that the machine is always turned off when there is no water supply. Additionally, regularly cleaning and maintaining your ice maker can help to prevent the build-up of ice and mold, ensuring optimal performance.
3. Can leaving an ice maker on without water cause damage to my home?
Leaving an ice maker on without water can potentially cause damage to your home if the appliance malfunctions and leaks water onto the floor. It can also pose a fire hazard if the motor overheats due to the lack of water.
4. How can I tell if my ice maker has been damaged due to lack of water?
Signs of potential damage to your ice maker due to the lack of water can include a decrease in ice production, unusual noises coming from the machine, and a change in the taste or quality of the ice produced. If you notice any of these signs, it’s important to turn off your ice maker and inspect the machine for any visible damage.
5. What should I do if I suspect my ice maker has been damaged?
If you suspect that your ice maker has been damaged due to the lack of water, it’s essential to contact a professional appliance repair technician to assess the extent of the damage and make any necessary repairs. Ignoring potential damage to your ice maker can lead to further issues and potentially result in the need for a costly replacement.
[ad_2]
- DIY Closet2 years ago
How to troubleshoot and reset the red light on your Aquaguard AG 3000E
- DIY Closet2 years ago
How to Install a Drop-In Sink Without Clips: A Step-by-Step Guide
- Bug Fixing1 year ago
Understanding the Cost of Furnace Collector Box Replacement: What to Expect
- DIY Closet1 year ago
Pergola Design: Understanding the Maximum Span for 6×6 Beams
- DIY Closet2 years ago
The Best Nails for Luan: A Comprehensive Guide
- Bug Fixing1 year ago
Pigtail vs Daisy Chain Outlets: Which is Better for Your Home?
- DIY Closet2 years ago
How to Build a Free Standing 6×6 Post Swing Set: A Step-by-Step Guide
- DIY Closet2 years ago
Understanding the Benefits of a 400 Amp Meter Base with Two 200 Amp Disconnects