DIY Closet
The Risks of Exposed Roof Sheathing: How Long is Too Long?
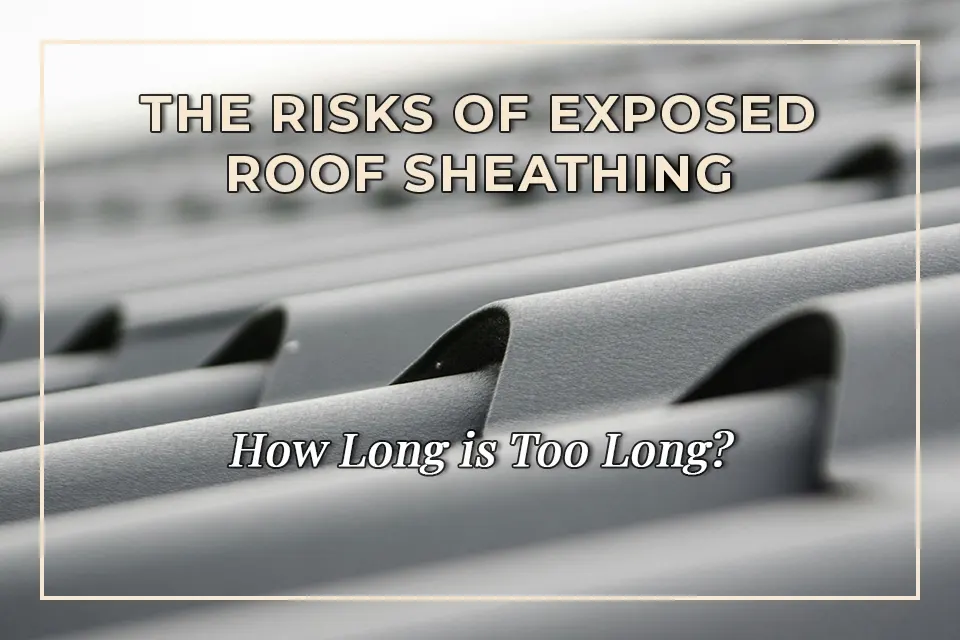
[ad_1]
In this article, we will discuss the risks associated with having exposed roof sheathing and how long it can be left exposed before causing potential damage to your roof and home. We will also provide some tips on how to prevent damage and protect your roof sheathing.
What are the Risks of Exposed Roof Sheathing?
Exposed roof sheathing can lead to a number of problems for your home. When the sheathing is left exposed to the elements, it can become damaged by moisture, leading to rot and decay. This can weaken the structure of your roof and potentially lead to leaks and water damage inside your home. In addition, exposed sheathing can also make your home more vulnerable to pests such as termites, who can easily access and infest the wood.
Furthermore, depending on the type of sheathing material used, exposure to UV rays can cause it to deteriorate more quickly, leading to the need for premature replacement. It’s important to address exposed sheathing promptly to prevent these potential risks.
How Long can Roof Sheathing be Left Exposed?
The length of time that roof sheathing can be left exposed before it becomes a problem depends on various factors such as the climate, the type of sheathing material, and the extent of the exposure. In general, it is best to avoid leaving roof sheathing exposed for an extended period of time as it increases the risk of damage and deterioration.
In most cases, roof sheathing should be covered with roofing materials within a few days to a week after installation to minimize the risks. If you are unable to do so, it’s important to take proactive steps to protect the sheathing from the elements, such as using temporary waterproof covers or tarpaulins, to prevent potential damage.
How can I Protect Exposed Roof Sheathing?
If you find yourself in a situation where your roof sheathing is exposed for an extended period of time, it is important to take steps to protect it from damage. One of the most effective ways to do so is by using temporary waterproof covers or tarps to shield the sheathing from rain, snow, and UV rays.
It’s also crucial to ensure that the sheathing is properly ventilated to prevent moisture buildup, which can accelerate decay and rot. Additionally, inspect the sheathing regularly for any signs of damage or deterioration and take prompt action to address any issues that arise.
What are the Implications of Ignoring Exposed Roof Sheathing?
Ignoring exposed roof sheathing can lead to significant repercussions for your home. If left untreated, the sheathing can become weakened, which may compromise the structural integrity of your roof. This can result in costly repairs and potentially even pose safety risks for you and your family.
In addition, the presence of exposed sheathing can make your home more susceptible to water damage and pest infestations, both of which can lead to further complications and expenses. It’s essential to address exposed roof sheathing promptly to prevent these issues from escalating.
Conclusion
Exposure to the elements can pose serious risks to roof sheathing, such as moisture damage, decay, and pest infestations. It is crucial to minimize the duration of exposure and take proactive measures to protect the sheathing from potential damage. Ignoring exposed sheathing can lead to structural problems and costly repairs for your home.
FAQs
Q: Can I use a tarp to cover exposed roof sheathing?
A: Yes, using a tarp or temporary waterproof cover can help protect the sheathing from moisture and UV rays. It’s important to secure the cover properly to prevent it from being blown off by the wind.
Q: How long can roof sheathing be left exposed before it starts to deteriorate?
A: The timeframe can vary depending on several factors, but generally, it’s best to avoid leaving the sheathing exposed for more than a week to minimize the risk of damage and deterioration.
Q: What are the signs of damage to roof sheathing that I should look out for?
A: Signs of damage may include discoloration, warping, soft spots, or visible decay. It’s important to inspect the sheathing regularly for any of these indicators and take action to address them promptly.
Q: Will insurance cover the costs of repairing damaged roof sheathing?
A: It’s best to check with your insurance provider to understand the coverage available for roof sheathing damage. The extent of coverage may depend on the cause of the damage and your specific policy.
Q: What are the risks of ignoring exposed roof sheathing?
A: Ignoring exposed roof sheathing can lead to structural problems, water damage, and pest infestations, which may result in costly repairs and safety hazards. It’s important to address exposed sheathing promptly to prevent these potential issues.
[ad_2]
DIY Closet
Why Do Window Sticks Extend Past Siding?
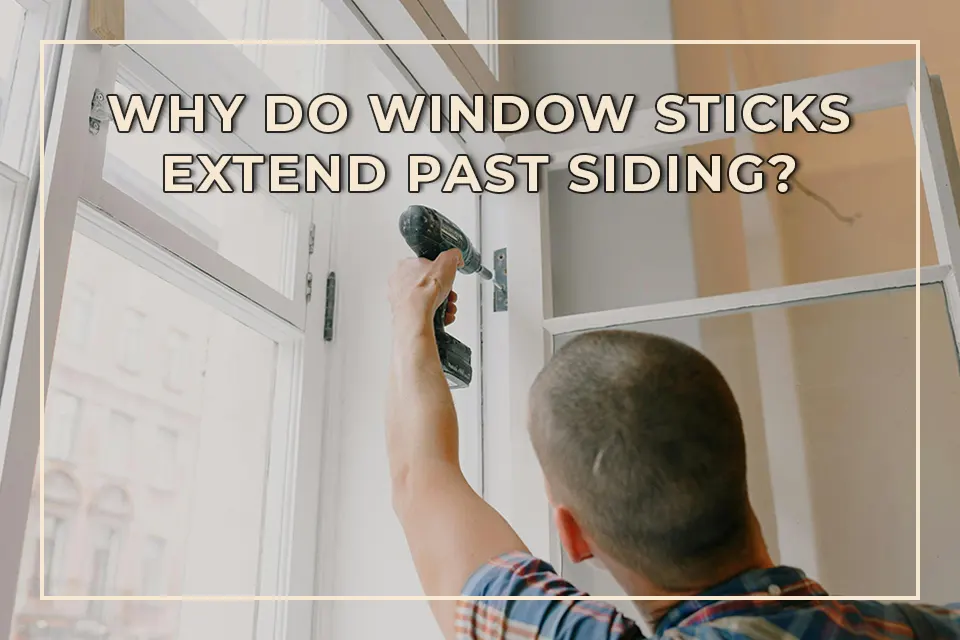
When renovating or building a home, you might notice that window sills or trim often extend beyond the siding. This seemingly odd feature serves practical and aesthetic purposes. Understanding why these elements are designed this way can enhance your home improvement skills and provide insight into effective exterior design.
Understanding the Construction Basics
Window sills and trim are key components in the installation of windows. They are designed to provide a finished appearance while also serving vital functional roles. The construction of windows involves various elements such as frames, sills, and surrounds, all of which contribute to a building’s integrity and aesthetics.
The extension of window sills beyond siding is a common practice that dates back to traditional building techniques. By extending the sills, builders ensured proper drainage, reduced water infiltration, and created a more aesthetically pleasing visual line. Understanding these basic construction aspects is crucial for anyone looking to undertake home improvement projects.
Reasons for Extension
There are several reasons window sticks extend past siding. One of the main purposes is to channel water away from the building’s structure. When rainwater falls, it can accumulate and seep into the seam between the window and siding. Extended sills help direct water away, reducing the risk of mold, rot, and other moisture-related issues.
Moreover, ensuring that the sills protrude past the siding creates a barrier that effectively prevents water from getting behind the window frame. This simple yet effective design principle can significantly prolong the lifespan of your windows and the siding adjacent to them, saving you potential repair costs in the long run.
Aesthetic Appeal
In addition to their practical uses, extended window sills provide an appealing aspect to the exterior design of a home. Architectural design often incorporates contrasting elements to create visual interest. By extending the sills, builders can add depth and dimension to the facade of a building.
This added dimension not only highlights the windows themselves but also creates shadows that can accentuate various architectural features. Depending on the style of the home, these extensions might contribute to a traditional, modern, or eclectic look. The aesthetics can heavily influence potential buyers’ perceptions during real estate transactions, making homes with well-designed exterior details more attractive.
Seal and Protection
Another important reason for extending window sills past the siding is the need for effective sealing. Properly installed window sills minimize gaps where cold air can enter and heat can escape, thereby improving the home’s energy efficiency. This is especially important in regions with extreme weather conditions.
When installing windows, it is crucial to use quality materials to seal the gaps thoroughly. This includes using caulk or other sealants that adhere well to both the window frame and siding. The extension not only accommodates this sealing but also pushes the water away from the more vulnerable junction where the window frame meets the siding.
Practical Installation Tips
If you’re considering a DIY window installation project and wondering about extending the window sills, there are some practical tips to keep in mind. First, ensure you measure your sills carefully before installation. Extensions should ideally extend about 1 to 2 inches beyond the siding. This will provide enough overhang to redirect water while maintaining a cohesive look.
Second, consider the material. Wooden sills may require sealing or painting to withstand the elements, while PVC or composite materials can offer durability without extensive upkeep. Always prioritize functionality alongside aesthetics during your installation process.
Additional Considerations
While extended window sills often provide numerous benefits, it’s worth noting that improper installation can create issues. If a window sill is too long, it can create a space for debris to accumulate, which can lead to moisture retention and attract pests. Therefore, striking a balance is key.
Whenever you opt for window extensions, take into account the specific requirements of your climate, architectural style, and desired aesthetic. The right proportions and materials can yield a functional yet visually appealing outcome.
Modern Innovations in Window Design
With advancements in technology and materials, there are numerous innovative options available for window installations today. Many manufacturers produce windows with integrated flashing systems that help direct water away without requiring significant overhangs. This can be incredibly beneficial for regions with heavy rainfall or snow.
In addition, new materials like fibreglass, vinyl, and advanced composites offer enhanced durability and low maintenance requirements, reducing the upkeep concerns associated with traditional wood. Wherever possible, opt for energy-efficient windows and materials to contribute to your home’s overall sustainability.
Conclusion
Understanding why window sills extend past siding is crucial for homeowners and DIY enthusiasts alike. Not only do these extensions enhance water management and energy efficiency, but they also contribute to a home’s aesthetic appeal. Proper installation of window sills ensures a functional and effective barrier against moisture while elevating the property’s overall appearance.
Ultimately, whether you’re planning a minor renovation or a substantial construction project, paying attention to the details—such as the alignment of window sills and siding—can lead to long-lasting benefits. From protecting your investment to improving your home’s features, recognizing the importance of these design elements can empower you in your home improvement journey.
FAQs
1. How much should a window sill extend past the siding?
Typically, a window sill should extend about 1 to 2 inches beyond the siding for optimal water drainage and aesthetic appeal.
2. What materials are best for window sills?
Durable materials such as vinyl, fibreglass, or treated wood can work well for window sills, each offering unique benefits in terms of maintenance and appearance.
3. Can I install window sills myself?
Yes, many homeowners can install window sills themselves, although it’s essential to follow proper guidelines and take accurate measurements for the best results.
4. How do extended window sills affect energy efficiency?
Extended window sills can help reduce air infiltration at windows, contributing to a more energy-efficient home by minimizing heat loss in winter and heat gain in summer.
5. Should I seal the gap between the window and the sill?
Yes, sealing the gap between the window and sill is crucial for preventing moisture infiltration and enhancing energy efficiency. Be sure to use quality sealants for the best results.
DIY Closet
Is Minwax Stain Suitable for Exterior Use?
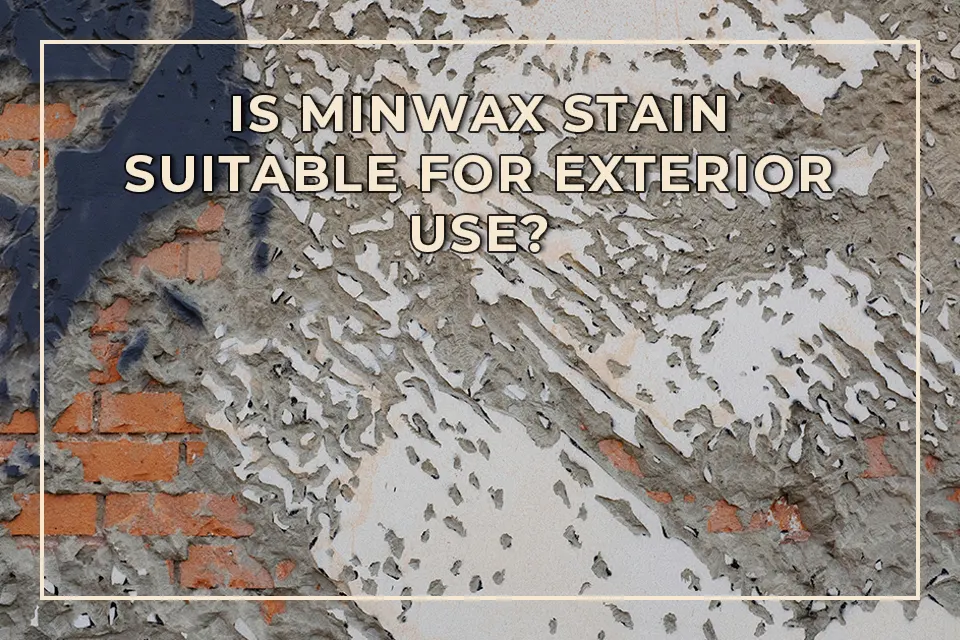
Minwax is a well-known brand that offers a variety of wood stains and finishes. Homeowners and DIY enthusiasts often wonder if Minwax stain is suitable for exterior use. This article delves into the capabilities of Minwax stains in outdoor settings, discussing their composition, applications, and best practices for ensuring lasting results.
Understanding Minwax Stains
Minwax offers a wide range of wood stains, primarily designed for indoor applications. Their products are popular for their rich colors and ease of use. Most Minwax stains are oil-based or water-based and are often chosen for furniture, cabinetry, and interior trim. However, using these products outdoors raises several concerns regarding their performance against weather elements.
Interior Versus Exterior Stains
The primary difference between interior and exterior stains lies in their formulation. Interior stains are optimal for protecting and enhancing the look of wood inside the house. They typically contain fewer protective agents against UV rays and moisture, making them less suitable for outdoor use. Conversely, exterior stains are formulated with special additives designed to withstand the elements, including sun, rain, and frost. This makes exterior stains more effective for outdoor projects. As such, it’s essential to evaluate what specific Minwax product you’re considering before using it outside.
What Makes a Stain Suitable for Exterior Use?
When considering a stain for outdoor applications, it’s crucial to look at key factors that determine its suitability:
- UV Protection: Outdoor stains must be able to resist fading and deterioration caused by sunlight. They usually contain chemical inhibitors that help protect the wood from ultraviolet damage.
- Water Resistance: Exterior stains often have properties that repel water, minimizing the risk of moisture-related issues such as warping, cracking, or mildew buildup. Good water resistance is essential for extending the lifespan of wooden surfaces that experience rain and snow.
- Durability: The best exterior stains offer a protective film that withstands wear and tear from various weather conditions. They’re designed to prevent chipping and peeling, which can occur when exposed to harsh elements.
Minwax Product Line and Their Suitability for Outdoors
While most Minwax stains are primarily intended for interior use, there are a few options available that can work for outdoor projects. For example, Minwax’s “Helmsman” line is specially formulated for exterior use. This line incorporates UV filters and water repellent properties, making it a suitable choice for outdoor furniture, decks, and fences.
Helmsman stains come in both oil-based and water-based formulations. The oil-based options provide excellent adhesion and depth of color but might require more extended drying times and cleaning with solvents. On the other hand, water-based formulations dry quickly and have less odor, making them easy to work with, particularly for those who are new to DIY projects.
Application Tips for Minwax Stains in Outdoor Settings
If you decide to use Minwax stain for an exterior project, consider these helpful tips for optimal results:
- Surface Preparation: Properly preparing the wood surface is critical. Clean the wood thoroughly to remove dirt and debris. Sanding the surface can enhance stain adhesion and lead to a smoother finish. Always follow the recommended directions for preparing the specific type of wood you’re working on.
- Weather Conditions: Choose a good day for your staining project. It’s best to work in mild temperatures and avoid high humidity. Ideally, wait for a dry day with little to no wind, as this can affect the drying process.
- Test First: Always conduct a small test area before applying the stain to the entire surface. This step will help you gauge how the wood reacts with the stain and allow you to make adjustments if necessary.
- Multiple Coats: Depending on the desired finish, you may find that multiple coats of stain are necessary. Make sure to let each coat dry fully before applying the next.
- Regular Maintenance: Even the best stains will require ongoing maintenance. Depending on weather exposure, consider reapplying the stain every couple of years to maintain its protective qualities.
Common Misconceptions About Minwax Stain
One common misconception is that all Minwax products are suitable for any exterior wood project. While some are marked for outdoor use, many of their stains lack the formulations needed to endure harsh outdoor conditions.
Another myth involves durability and longevity. While many believe that a single application is sufficient to protect outdoor wood, regular maintenance is essential. Depending on your local climate, you may need to reapply stain sooner than expected.
Pros and Cons of Using Minwax Stains for Exterior Projects
Pros
- Ease of Application: Minwax stains are user-friendly, making them suitable for DIYers. They are often easy to apply and require minimal tools.
- Wide Variety: Minwax offers a broad range of colors, allowing homeowners to find a finish that complements their home exterior.
- Accessibility: Minwax products are readily available in stores and online, making it easy for users to find what they need.
Cons
- Limited Options: Most of Minwax’s stains are primarily geared toward indoor use, exposing a limitation for outdoor projects.
- Maintenance: Exterior projects will require ongoing maintenance to ensure the wood remains protected from the elements.
- Potential Peeling: If not correctly applied, stains can peel or chip, particularly on surfaces exposed directly to sunlight or moisture.
Conclusion
While Minwax offers some products that can be suitable for outdoor use, particularly the Helmsman line, most of their stains are intended for indoor applications. When working on exterior wood projects, it’s essential to choose products that provide UV protection, water resistance, and durability suited for outdoor conditions. By selecting the right stain and following proper application techniques, you can achieve beautiful results that enhance your home’s exterior while ensuring long-lasting protection.
FAQs
1. Can I use regular Minwax stain for my outdoor furniture?
Using regular Minwax stain on outdoor furniture is not recommended as it lacks the necessary protection against UV rays and moisture. It is best to use Minwax Helmsman or another exterior-specific stain instead.
2. How often should I reapply exterior stain?
The frequency of reapplication depends on various factors including climate and the type of wood. Typically, exterior stains should be reapplied every 1 to 3 years, depending on exposure.
3. Is water-based stain better than oil-based for outdoor use?
Water-based stains dry faster and have less odor, making them easier to use. However, oil-based stains generally provide better penetration and durability for outdoor surfaces. The choice often depends on personal preference.
4. Will exterior Minwax stains protect against mold and mildew?
While exterior Minwax stains contain some resistance to mold and mildew, it is essential to maintain the wood’s surface and clean it regularly. Stains do not eliminate the need for ongoing care.
5. Can Minwax stains be used on composite decking?
Minwax stains are typically designed for natural wood surfaces. Composite decking may require specialized stains or coatings designed specifically for synthetic materials. Always check the manufacturer’s recommendations.
DIY Closet
How Can You Use Thinset to Fill Low Spots in Your Flooring?
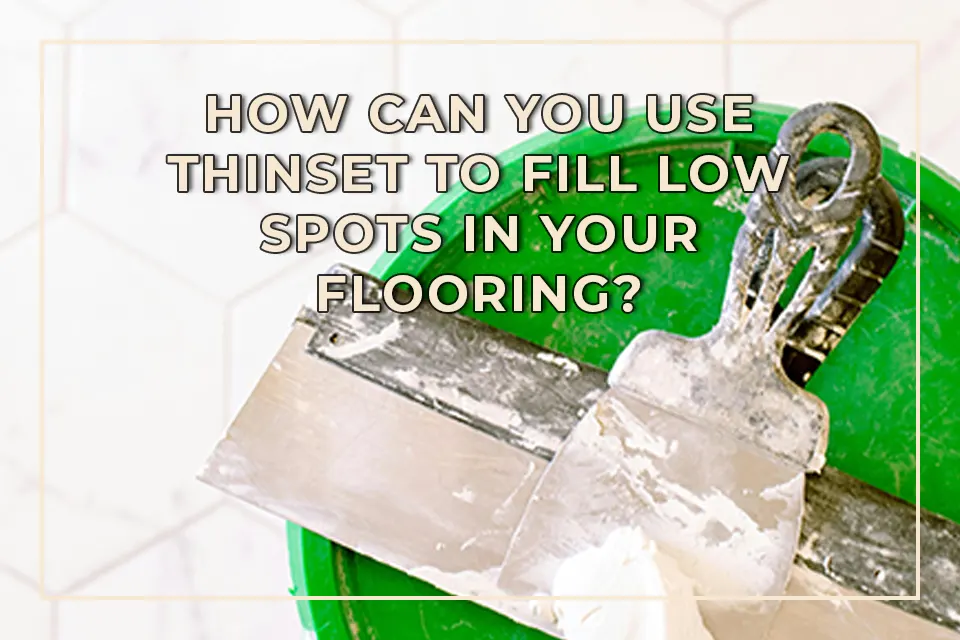
Thinset is a versatile adhesive often used in tile installation, but it can also be an effective solution for leveling out low spots in flooring. This article will guide you through the process of using thinset to fill low areas, enhancing the overall look and durability of your flooring.
Understanding Thinset
Thinset is a cement-based adhesive primarily used in tile applications. It’s formulated to hold tiles firmly in place and is commonly mixed with water to achieve a suitable consistency. Thinset contains ingredients that provide strong adhesion, flexibility, and resistance to moisture, making it an ideal option for flooring projects. Besides being a strong adhesive, it also serves as a leveling agent.
Before using thinset for filling low spots, it’s essential to understand that it should be applied as a mortar bed and not more than a few eighths of an inch thick in a single layer. For larger voids, multiple applications may be necessary. When used correctly, thinset can provide a smooth, even surface, creating an excellent foundation for tiles or other flooring materials.
Preparing the Area
To achieve the best results when filling low spots with thinset, preparing the area is crucial. Start by removing any existing flooring or covering if necessary, as this will allow you to access the subfloor. Clean the surface thoroughly, removing dirt, dust, grease, and any other debris that could hinder the adhesion of the thinset.
Inspect the subfloor for any significant damage or structural issues. If you identify serious concerns, such as rot or significant warping, it’s wise to address those problems before applying thinset. Once the subfloor is clean and dry, you can begin marking low spots for filling.
Identifying Low Spots
Before you start applying thinset, you need to identify the low spots in your flooring. A simple way to check for uneven areas involves using a long level or straightedge. Place it on the floor and observe the gaps underneath. A gap of more than an eighth of an inch indicates a low spot that needs leveling.
Mark these low areas with a chalk line or a pen, making it easier to keep track during your application of thinset. It’s often helpful to measure the depth of each low spot. Measuring helps you know how much thinset to apply and makes it easier to mix the right amount.
Mixing Thinset Properly
Properly mixing thinset is critical to ensure it performs well as a leveling agent. Start by following the manufacturer’s instructions on the thinset bag, as the ratios can vary between brands. Generally, thinset is mixed with water in a bucket.
Begin by adding water to the bucket, then gradually add the thinset powder while stirring continuously. Use a mixing paddle attached to a drill for a smooth consistency, avoiding lumps that can impede proper application. Aim for a peanut butter-like texture: not too runny but not overly thick.
Allow the mixed thinset to slake, or sit, for about 10-15 minutes. This process enables the chemicals in the thinset to activate fully. After slaking, stir the mixture again for a few moments before applying it to the low spots.
Applying Thinset to Low Spots
With your thinset prepared, it’s time to start filling the low spots. Using a trowel or a float, begin applying the thinset to the marked areas of your flooring. Work in small sections, focusing on one low spot at a time to ensure it’s evenly filled and smooth.
Use the trowel to spread the thinset, ensuring it fills the void completely and is leveled off with surrounding areas. It’s crucial to keep a consistent thickness — usually around 1/8 inch at most. For larger holes or uneven areas, you can build up more layers, letting each layer cure before adding the next.
After applying thinset, it’s important to smooth out the edges and avoid any uneven ridges or bumps. You can use the flat side of the trowel to flatten and feather the edges for a more seamless transition between the filled and unfilled areas.
Curing the Thinset
After applying thinset, allow it to cure properly. Thinset usually takes about 24 to 48 hours to dry fully, but this can vary based on humidity and temperature conditions. It’s essential not to lay any flooring over the thinset until it’s completely cured to ensure solid adhesion and optimal results.
To check if the thinset is dry, lightly tap or press on the surface. It should feel solid and not shift under pressure. Avoid jumping the gun; rushing this step could lead to cracks or improperly adhered flooring later on.
Finishing Touches
Once the thinset is fully cured, the next step is to prepare the surface for the final flooring material. Start by sanding down any uneven areas using sanding blocks or a pole sander to achieve a smooth finish. This will help avoid any bumps in the final layer of your flooring.
After sanding, thoroughly clean the area to remove any dust or debris. You can now proceed with your flooring installation, whether you are laying tile, laminate, or hardwood flooring. Be sure to follow the manufacturer’s instructions for installing your specific flooring type, particularly regarding adhesives and necessary underlayments.
Conclusion
Utilizing thinset to fill low spots in your flooring is an effective DIY solution that can save you time and money while maintaining a professional finish. By preparing your area, identifying low spots, and carefully mixing and applying thinset, you can create a smooth and even subfloor for any flooring material. While it might require some additional patience during the curing and finishing processes, the results will make the effort worthwhile. A well-leveled floor not only improves aesthetics but also promotes longevity and comfort in your living space.
FAQs
1. Can I use thinset on a concrete floor?
Yes, thinset can be applied on concrete floors. Just ensure that the surface is clean and free from any debris before applying it.
2. How thick can I apply thinset when filling low spots?
Ideally, you should not apply more than 1/8 inch in a single layer. For deeper low spots, it’s best to apply multiple layers, allowing each to cure fully before adding the next.
3. What tools do I need to apply thinset?
You’ll need a mixing bucket, a mixing paddle, a trowel or float, a long level or straightedge, and possibly a sanding block or pole sander for finishing.
4. How do I know when the thinset is cured?
The thinset is considered cured when it is solid and does not shift under your touch. This typically takes 24 to 48 hours, depending on conditions.
5. Can I apply thinset over painted floors?
It’s not recommended to apply thinset over painted floors, as it may affect adhesion. It’s best to remove loose paint and ensure the surface is bare and clean before applying thinset.
- DIY Closet1 year ago
How to troubleshoot and reset the red light on your Aquaguard AG 3000E
- DIY Closet1 year ago
How to Install a Drop-In Sink Without Clips: A Step-by-Step Guide
- Bug Fixing1 year ago
Understanding the Cost of Furnace Collector Box Replacement: What to Expect
- DIY Closet1 year ago
Pergola Design: Understanding the Maximum Span for 6×6 Beams
- DIY Closet1 year ago
The Best Nails for Luan: A Comprehensive Guide
- Bug Fixing1 year ago
Pigtail vs Daisy Chain Outlets: Which is Better for Your Home?
- DIY Closet2 years ago
How to Build a Free Standing 6×6 Post Swing Set: A Step-by-Step Guide
- DIY Closet1 year ago
Understanding the Benefits of a 400 Amp Meter Base with Two 200 Amp Disconnects